Your Insert Molding Partner
RCT MFG is a leading insert molding manufacturer. Our services include injection molding production, custom injection molds, and overmolding. We also offer optional surface treatments to meet your specific requirements. Our one-stop part forming services are designed to deliver high quality and efficient production, making us the first choice for companies looking for reliable and cost-effective solutions. With competitive prices and fast delivery times, RCT MFG is your trusted partner for market testing and mass production needs.
At RCT MFG, we offer in-depth, comprehensive insert molding services and handle a variety of plastic grades, including consumer and engineering grade plastics. We also operate 21 different molding machines, including robotic gate pickers, automated conveyors, coordinate measuring machines (CMMs), and vertical presses using rotary tables and engineering-grade plastics. Our state-of-the-art equipment and years of experience enable us to handle the most complex tasks reliably and precisely.
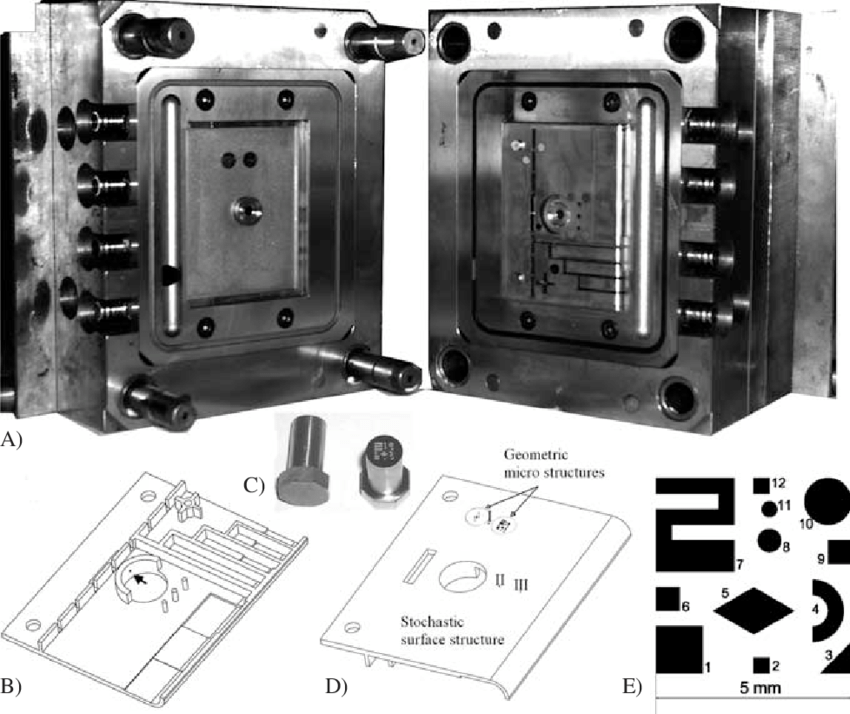
RCT MFG Insert Injection Molding Capabilities
Standards | Description |
---|---|
Maximum Part Size | 1200×1000×500 mm; 47.2×39.4×19.7 in. |
Minimum Part Size | 1×1×1 mm; 0.039×0.039×0.039 in. |
Part to Part Repeatability | +/- 0.1 mm; +/- 0.0039 in. |
Mold Cavity Tolerances | +/- 0.05 mm; +/- 0.002 in. |
Available Mold Types | Steel and aluminum tooling. Production grade we provide: Under 1000 cycles, under 5000 cycles, under 30,000 cycles, and over 100,000 cycles |
Machines Available | Single cavity, multi-cavity, and family molds, 50 to 500 press tonnage |
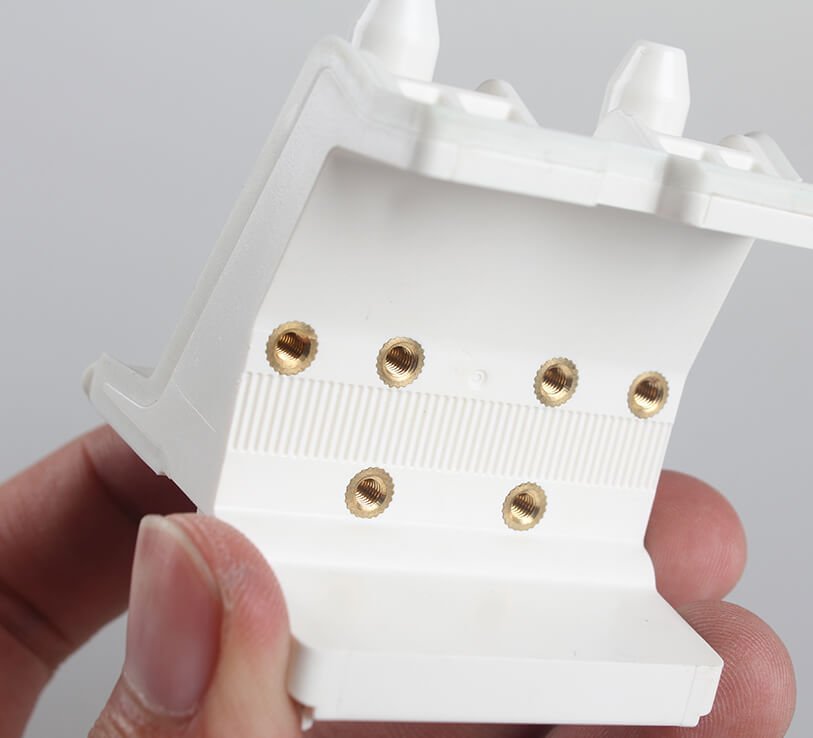
Insert Injection Molding VS Injection Molding
Insert injection molding and injection molding are similar processes, but inserts add durability and strength. For example, two plastic components that mate together to form a hinge can be made with standard injection molding. If the components are going to be used in a weight-bearing application, however, metal inserts are needed to create more stability. Components made with insert injection molding are stronger than standard plastic parts but still lighter and less prone to corrosion than metal.
Overall, inserts are used in applications where characteristics of both the plastic and the insert material are needed.
Insert Injection Molding VS Overmolding
Overmolding is a compounding process that molds an additional layer of plastic over a previously molded component. Additional inserts are not incorporated into the component for the purpose of augmenting it like they are during insert injection molding, which is also only a one-step process.
At RCT MFG, we offer injection molding, insert injection molding, and overmolding to address our customer needs.
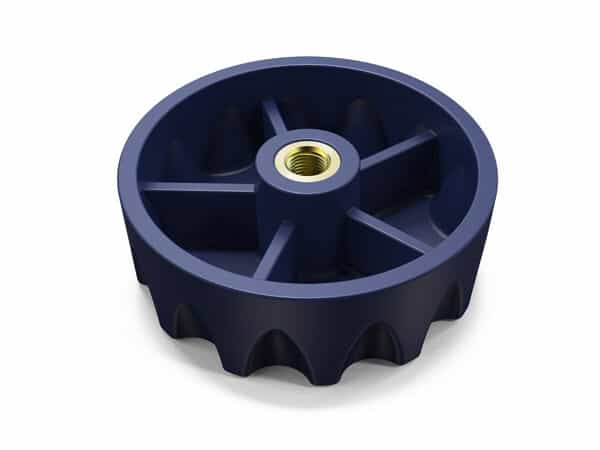
Let's Start A New Project Today
Why Combine Metal and Plastics?
Metallic parts encapsulated by plastic can provide a wide range of benefits to a process or application, such as improving reliability, impact resistance, and weight. Most plastics withstand exposure to moisture, chemicals, and ultraviolet light, meaning they can better protect metal from the elements.
Another benefit is increased part compatibility. Some metals just don’t work well together, and direct contact may cause issues like corrosion or degradation. With insert molding, plastic covers mating part surfaces.
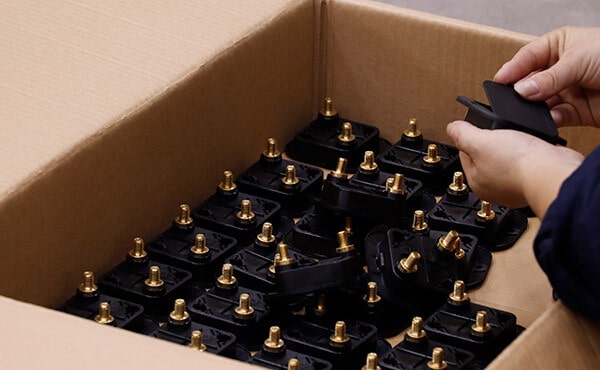
Insert Injection Molding Benefits
Insert Molding is an injection molding process that works especially well for parts that have threaded holes. It can also help you create better wheels, pulleys, fan blades, and other similar parts. Done correctly, insert molding can help:
- Eliminate assembly: You can make insert molded parts all at once instead of having to do assembly after the fact.
- Reduce costs: Insert molding costs more than standard injection molding, but the costs are usually offset by the fact that you no longer need to do post-assembly.
- Lower the size and weight of the part: A plastic part with a metal insert is generally lighter than an all-metal part.
- Improve reliability: Metal mold inserts will guarantee the function of threads and mitigate wear and tear over the part's life.
- Improve part strength: Because it’s a “one-shot” process, it can produce stronger parts than overmolding and other processes.
Material Options for Insert Molding
RCT MFG's Insert Molding service encompasses meticulous material selection, spanning from standard thermoplastics to exotic resins. Our expertise allows for numerous combinations of Insert Molding materials and substrates. Here are some of the most prevalent materials we utilize in the plastic Insert Molding process.
Tooling Materials
Prior to commencing the overmolding process for low or high-volume production, high-tolerance CNC machined tooling is essential. The most used materials include:
Tool Steel: P20, H13, S7, NAK80, S136, S136H, 718, 718H, 738
Stainless Steel: 420, NAK80, S136, 316L, 316, 301, 303, 304
Aluminum: 6061, 5052, 7075
Plastic Materials
The plastic injection molding service offers a diverse selection of materials, each possessing unique properties such as impact strength, rigidity, thermal resistance, chemical resistance, and more.
ABS, Nylon(PA), PC, PVC, PU, PMMA, PP, PEEK, PE, HDPE, PS, POM
Additives and Fibers
When standard plastic materials fail to meet the requirements of custom injection molding parts, additives and fibers can be incorporated to enhance both aesthetic and functional properties. These additional elements provide supplementary features for your injection molded parts.
UV absorbers, Colorants, Flame retardants, Glass fibers, Plasticizers
Inserts
Inserts are positioned onto the mold cores, either manually or via an automated mechanism, prior to the mold halves being sealed. Subsequently, plastic pellets are heated until they melt, enveloping the inserts as the mold closes. Once the molten plastic solidifies, indicating the plastic has set, the molded parts are ejected. This results in the inserts being securely embedded within the solidified plastic components.
Brass, Stainless Steel, Aluminum
Surface Finishing of Insert Molding
The services for insert molded parts extend beyond their cooling and ejection from the mold. We offer a variety of surface finishing and post-processing treatments to enhance both the functionality and aesthetics of the parts. At RCT MFG, some of the prevalent surface finishing options for insert molded components are:
Glossy
A-grade finishes are achieved through a diamond buffing process, resulting in shiny and glossy surfaces on injection molded parts.
Semi-glossy
B-grade finishes employ grit sandpaper to create parts with a slightly rougher texture compared to grade A finishes. Custom molded plastic parts subjected to B-grade finishing exhibit a matte surface texture.
Matte
C-grade finishes utilize grit sanding stones to generate a rough and uneven surface texture. Injection plastic parts subjected to C-grade finishing exhibit a matte surface texture.
Texured
D-grade finishes employ grit along with dry glass beads or oxide to create a highly rough textured finish. Depending on the material utilized, products may exhibit a satin or dull finish.
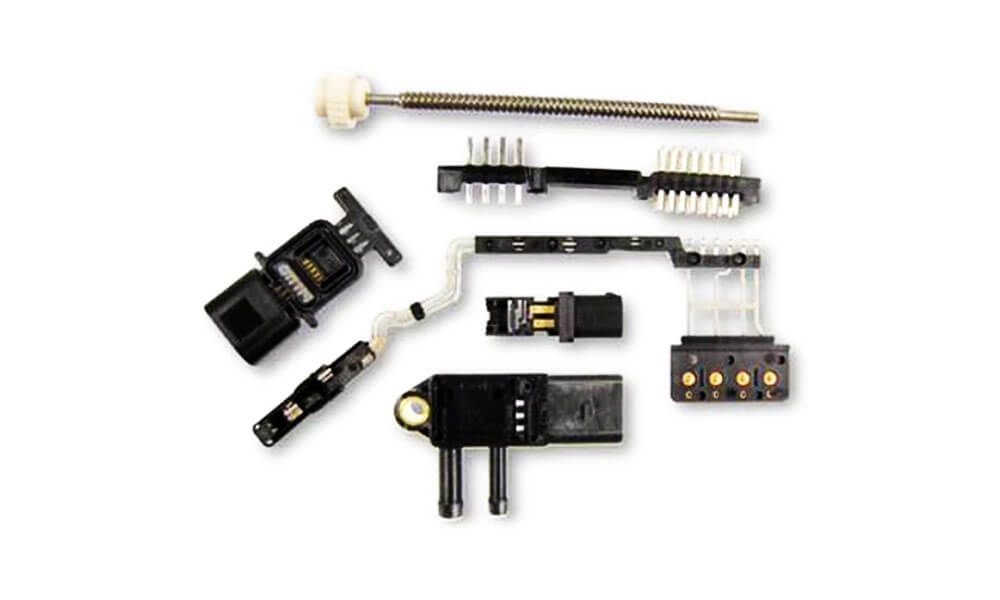
Applications & Uses for Plastic Injection Inserts
RCT MFG works with leading manufacturers from different industries to support growing demands and streamline their supply chain. The digitalization of our custom injection molding services helps more and more manufacturers bring their idea to products.
Insert molding metal inserts are derived directly from insert injection materials and are regularly used in a wide range of industries including: aerospace, medical, defense, electronics, industrial and consumer markets. The applications for metal inserts for plastic parts, include:
- Screws
- Studs
- Contacts
- Clips
- Spring contacts
- Pins
- Surface mount pads
- And more