Our Service
Rapid Tooling is one of the most-effective means of bridge tooling and low-volume mold production. RCT MFG delivers one of the best rapid tooling technologies to cater for low to medium volume manufacturing needs at low cost prices. Our rapid tooling process is optimized to produce you with quality injection-molded parts of both simple and complex geometries in real materials in the quickest possible timeframes.
At RCT MFG, we are able to run hand-loading inserts for ultra-low volume demands. We also offer comprehensive support for rapid tooling and provide value-adding solutions that range from product design assistance (DFM) to material selection, product structure optimization, mold design detail, flow analysis and other post-molding services (polishing, texturing and sandblasting) that will help to put you in pole position to introduce your concept to the market in only a number of weeks.
RCT MFG’s Rapid tooling uses a number of interchangeable mold base tooling to simplify complex tooling structure. We work with an interesting range of tooling in Aluminum, P20, NAK80, S136H and other materials. Our tooling life ranges from 5000 to 500000 shot depending on the geometry and simplicity of the part and the material used. Our in-house capability and experience also means that we are able to deliver excellent quality end-use parts at faster and cost-effective rates.
Rapid tooling can deliver about 40-50 percent cost and time savings over traditional molding techniques. Our tooling lead time is as quick as 5-20 days based on the final product to be produced and tool structure.
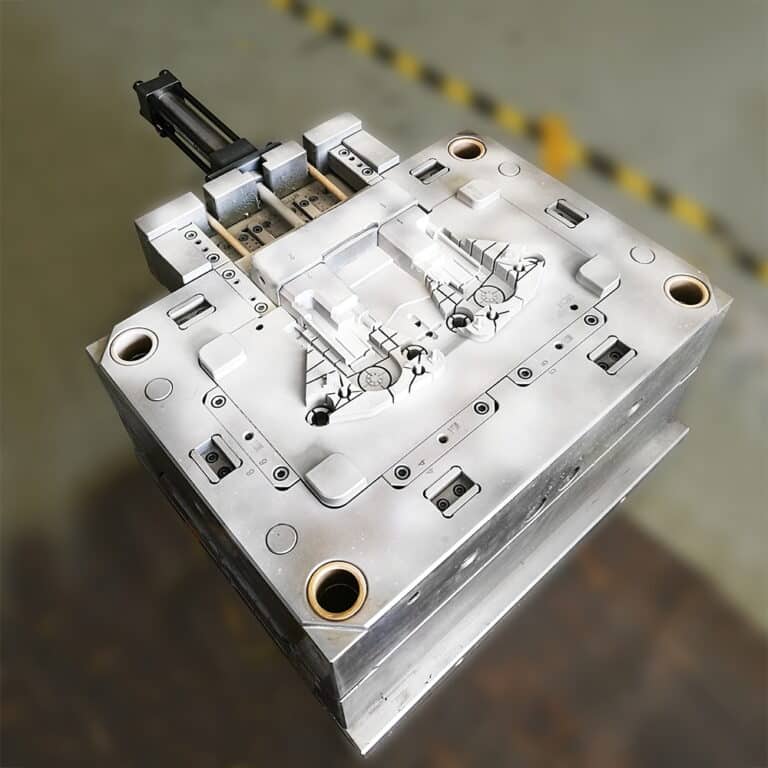
How Does Rapid Tooling Work?
RCT MFG offers a unique rapid tooling system. A single master machinist is responsible for your tool from start to finish. Using modular mold bases and P20 tool steel, a machinist can produce a finished mold in as little as ten days from the approval of design drawings. These molds use standard plastic resins and fillers to make fully functional finished parts in relatively limited quantities. There are many advantages to rapid tooling. Finished parts can be used for prototypes, product testing and certification, and as bridge production towards higher volumes. Rapid tooling injection molding also helps our clients to limit their financial exposure to new designs.
Why do We Need Rapid Tooling?
1. While other prototyping processes such as 3D printing, CNC machining, or complex molding often enable faster and cheaper prototyping, the main advantage of rapid machining is the process and materials.
2. Rapid Tooling can use actual production materials to help customers get a clearer picture of whether these parts will meet their standards in production, allowing you to test and confirm that you have selected the correct material.
3. We can also use rapid tooling to test production parameters, and engineers and designers can then find many previously unnoticed vulnerabilities and implement redesigns or other measures to prevent problems with the final part.
4. There are many other reasons for choosing rapid tooling, besides the prototyping and testing already mentioned. The main thing is the low cost, fast and efficient manufacture of injection molded parts.
5. The speed advantage enables you to get parts to market quickly, and the cost advantage enables market testing and means it is suitable for mass production.
Start your next project
What is rapid tooling?
Rapid Tooling is also called bridge mold, prototype mold or low volume production mold. The most distinctive of rapid tooling is that we apply the MUD(Master United Die) to the mold base, which means many cavities and cores inserts share one same mold base. In this way, the cost of mold base is more affordable and the lead time will be greatly reduced.
For the tooling structure, we have different designs based on different quantities. For example, if your only have a few hundred manufacturing parts demand, we will design hand loading insert or use post machining tool instead of the complex tooling structure and machining.
Usually, the tooling life is about 100,000 shots for rapid tooling. It also depends upon the structure of the tooling. For simple structure tooling, the tooling life can be up to 500,000 shots.
Compared with the traditional mold making, Rapid tooling can help you save 40% to 50% of the cost and 40% to 60% of the time. On top of that, Wintech can provide DFM (design-for-manufacture) report to our customer to analyze product structure, tooling building feasibility and potential quality risk. In this way, the tooling is safer. Our tooling lead time is about 5 to 25 calendar days based different product and tool structures.
What metal material are used for rapid tooling?
Aluminum 7075
Aluminum 7075 is the best choice for simple geometry product and low volume production requirement, such as 5k~10k quantity shots. By using AL-7075, the surface can be textured and polished to normal smoothness standard, but cannot meet high glossy surface request. The machining of Aluminum 7075 tool can be much faster because this material is softer and has better machinability. Besides, the machining cost will be reduced accordingly. Generally speaking, Al-7075 is the best metal material, the fastest and affordable way to make rapid tool.
P20
P20 material is commonly-used in rapid tooling. It is one of the most widely-used tooling steels in the world. P20 works for great majority of product’s dimension, surface finishing and part geometry. Depending on different part size, molding resin and tooling structure, the tooling life can be up to 200k.
S136H and NAK80
These two materials are commonly used for the high glossy product. The hardness is about HRC35~38, the tooling life can be up to 300k~500k owe to its higher hardness.
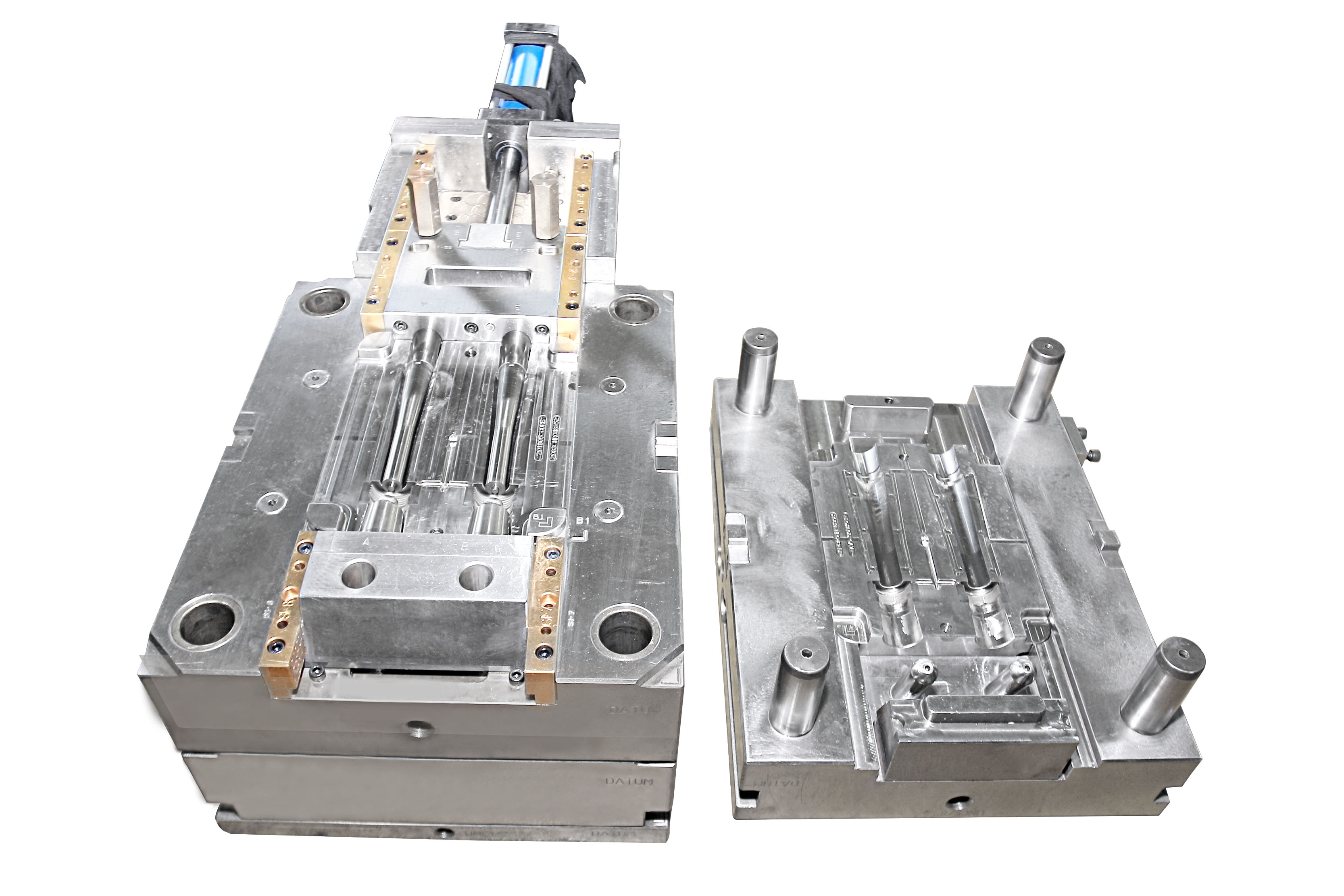
Advantages of Rapid Tooling
It is acknowledged that the main reason people manufacture rapid tooling is for testing and validation of parts in the prototyping stages of new product development. Compared with other machining methods, rapid tooling owns its main advantages on its process and materials. Rapid tooling allows you to know how the parts will act in real-world applications and enable you to test and confirm you have made the correct material choices.
Besides that, fast production time and lower cost are the points that have triggered interested among the customers.
Request Your Rapid Tooling Quote Today
After receiving your drawings, our engineers will analyze your custom parts right away. We actively work with you to clarify all details before providing a quote that is both economical and accurate.