Professional sheet metal manufacturing
RCT MFG is an experienced fabricator of sheet metal products. We are equipped to produce and assemble customized sheet metal components with exacting precision. This includes fabrication of the simplest parts and the most complex assemblies, in large or small quantities. Rather than offering limited options, our extensive sheet fabrication capabilities allow us to provide effective manufacturing solutions for your exact needs. When manufacturing custom products, our machines are compatible with multiple different kinds of metal, sheet lengths, and thicknesses. RCT MFG has the ability to produce long or short runs of these custom laser cut sheet metal products. Often, fabricated sheet metal components can be used in prototyping or for large scale production operations.
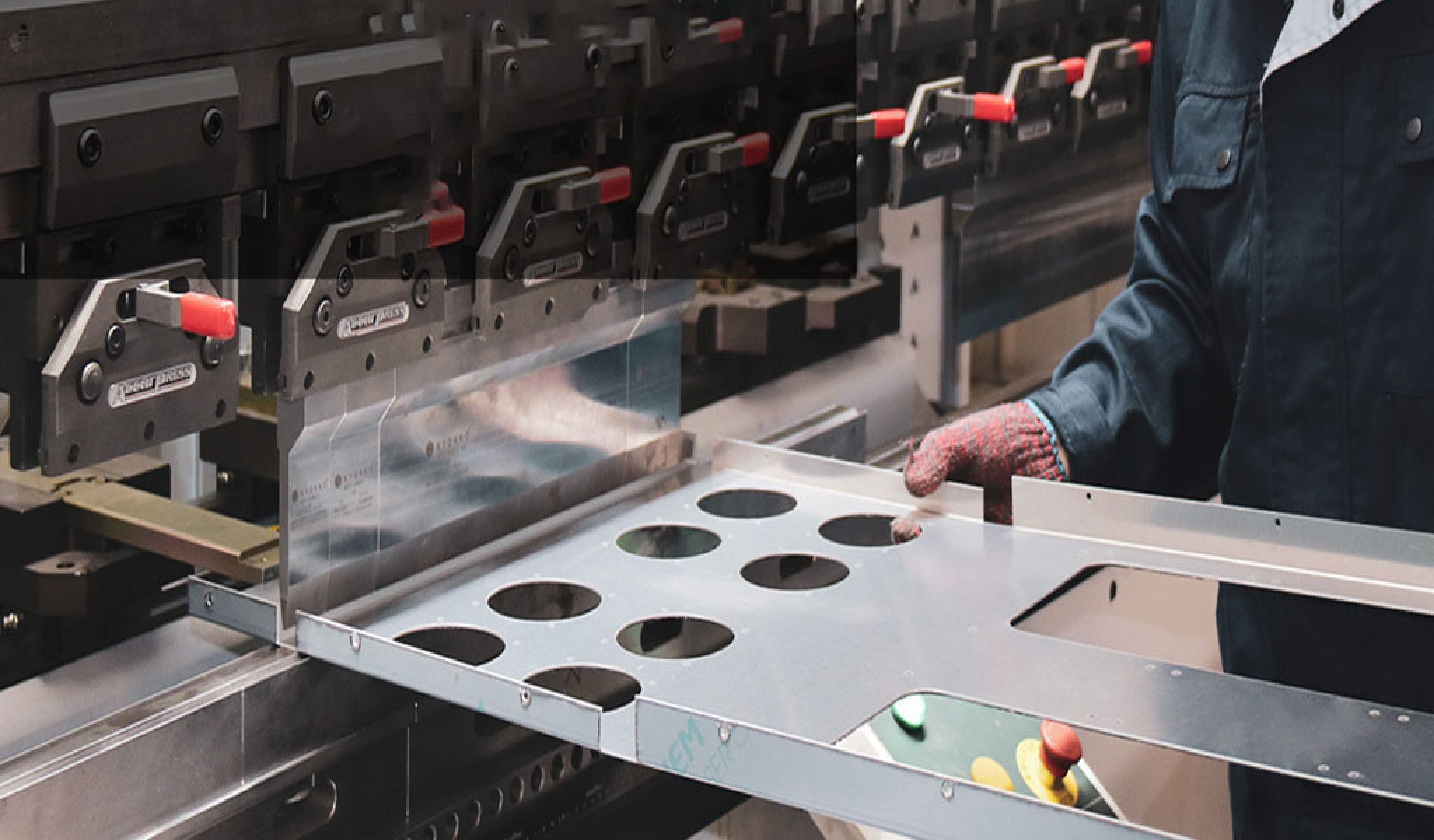
Our sheet metal services capabilities
RCT MFG takes on prototype and production sheet metal services and cutting.We can support one-offs, batch production and ongoing call-off orders in line with your requirements. We take on challenging complex jobs, be it complex part geometry, specialist materials, extremely tight tolerances or specialist finishing. We have earned our reputation amongst the world's leading companies for high-quality and precision sheet metal services , working on the very latest of technologies.
Laser Cutting
Laser cutting is a technology that directs a high-power laser to cut sheet metals, offering precision, fast processing, and the ability to create intricate designs with smooth finishes and tight tolerances.
Metal Bending
Bending is a versatile sheet metal fabrication process that creates V-shape, U-shape, and channel shapes in materials, providing high precision and repeatability with minimal setup cost. Perfect for complex geometries.
Metal Stamping
Sheet metal stamping is also known as pressing and involves placing a flat sheet into a press. This is a high volume, low-cost, and fast process for producing identical parts. Sheet metal stamping can also be performed in conjunction with other metal shaping operations for easy manufacturing.
Capabilities
Feature | Description |
---|---|
Blank Size |
10’ x 20’ (3.05 m x 6.10 m). We accommodate larger part volumes upon request. |
Standard Lead Time |
3 business days |
Sheet Thickness |
0.024” - 0.250” typical. We accommodate thicker or thinner gauges upon request. |
General Tolerances |
For single planes or flat parts, +/- 0.010” on edge to edge, edge to hole, and hole to hole features; +/- 0.010” on bend to edge/hole features. For multi-planed bent parts, +/- 0.030” for hole to hole/edge, edge to edge, and over-formed parts; +/- 1 degree for bend angles. |
Braking (Hydraulic) |
10’ length, fingers from 3” - 6” |
Braking (Magnetic) |
6 tons of magnetic pull across the entire beam, 5/8″ minimum reverse bend |
Punching |
2″ diameter hole capacity, or larger upon request |
Welding |
Welded edges and seams, weldments, and assemblies |
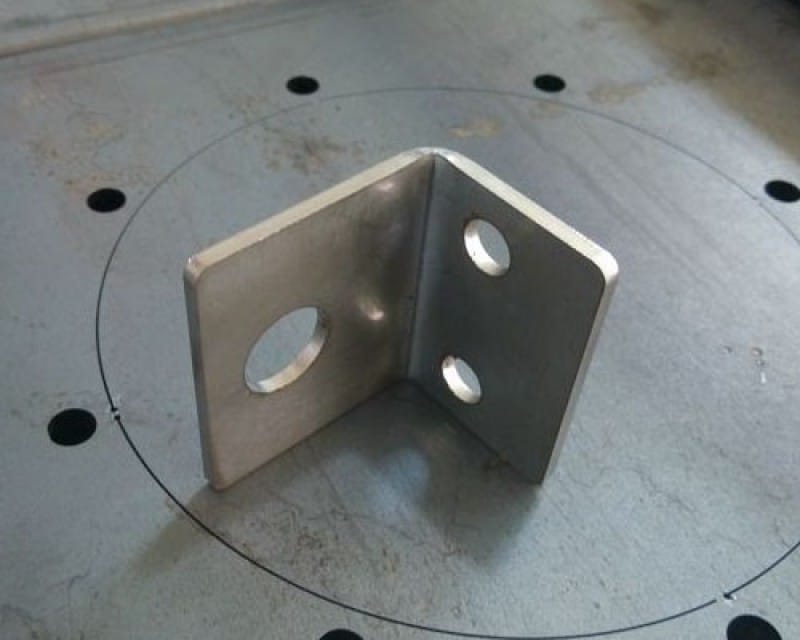
How RCT MFG Sheet Metal Fabrication Works
RCT MFG's custom sheet metal fabrication services utilize the top sheet metal fabricators in China and around the world. The sheet metal fabricator first converts the CAD and drawing data into machine code. Then, a laser cutter, water jet, or plasma cutter will precisely remove the sheet metal material. Corner bends and features are formed into the raw material using press brakes, punches, and dies. If any assembly or post-processing is required, our sheet metal fabricators will weld, add inserts, or finish the part.
The efficiency and high precision of sheet metal fabrication, combined with RCT MFG's wide range of materials, various sheet metal fabricators, and post-processing options, means you can get a part for any application. Sheet metal applications include aerospace, defense, automotive, energy, industrial, medical, dental, and consumer products.
What is Sheet Metal Fabrication?
Sheet metal fabrication is the basic process of manufacturing metal products. It involves forming metal sheets into desired shapes and sizes. Cutting, forming, and finishing are three methods of metal fabrication.
Sheet metal fabrication is used in countless industries, from the appliance industry, computer electronics, and railroads to aerospace, agriculture, and even the medical industry. Sheet metal is the building block of almost everything we touch on a daily basis. From cars to washing machines and I-beams in buildings, it is everywhere. It is hard to name an industry that does not use sheet metal fabrication in the production of its parts and products.
Materials Used in Precision Sheet Metal Fabrication Processes
Sheet metal fabrication processes can accommodate a wide variety of materials, each suitable for different parts and production requirements. Understanding the properties of potential material choices is essential to determining the right material for a particular project.
1. Aluminum: Aluminum sheet thicknesses range from 0.008 to 0.25 inches. Because aluminum increases in strength at ultra-low temperatures, it is ideal for cryogenic applications such as aerospace and cold storage operations. Its strength, durability, and thermal properties also make it well suited for use in many other industrial applications, including military armor, power cords, radiators, and bakeware.
2. Cold-rolled steel: Cold-rolled steel has an extremely high plastic strain ratio, meaning it does not get thicker or thinner when stretched or compressed. Additionally, it has a smooth surface that is easy to keep clean. This quality makes it an excellent building material for furniture, filing cabinets, automobiles, and appliances.
3. Hot-rolled steel: Because of its high strength, hot-rolled steel is used in a variety of construction applications, including shipbuilding, buildings, and bridges. This type of steel resists damage and degradation from atmospheric corrosion, extreme pressures, and high temperatures.
4. Galvanized Steel: Galvanized steel has an outer layer of zinc coating that creates a matte gray surface that protects the steel and prevents it from corroding. According to the National Galvanizers Association, the coating can make the material nearly 100 times more corrosion-resistant. In addition to being corrosion-resistant, this steel is also very durable, recyclable, and formable.
5. Stainless Steel: Stainless steel comes in several variations, all of which have some degree of corrosion resistance. This inherent quality is due to the material's composition, specifically the presence of chromium. The alloy may also contain other metallic and non-metallic elements, such as molybdenum, nickel, titanium, and niobium, to enhance certain material properties, including formability and corrosion resistance. Because the material is easy to clean and sterilize, it is ideal for use in food preparation, medical, pharmaceutical, and other sensitive applications.
Our engineers are familiar with the properties of all of the above materials. They can help customers select the right material when working with us on a sheet metal fabrication project.
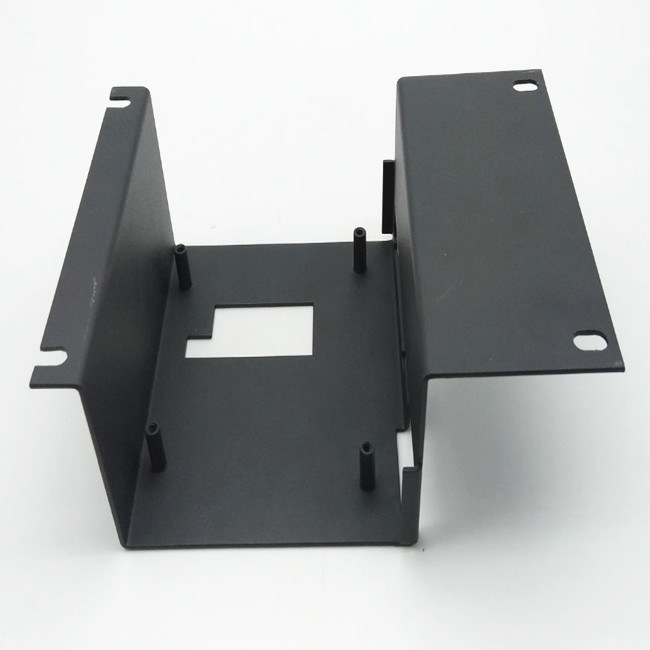
Sheet Metal Applications
Sheet metal is a versatile manufacturing process for a range of metal components. The process can support high-volume commodity products and low-volume, one-of-a-kind applications. Common sheet metal parts include:
1. Agriculture / Farming
2. Automobile
3. Aerospace
4. Construction
5. Electronics
6. Heavy Equipment
7. Manufacturing
8. Military
9. Railroad
10. Warehousing
One of the advantages of sheet metal fabrication is that its applications are almost endless. You almost certainly use a product manufactured with sheet metal every day, from your car to your laptop.
Sheet Metal Finishes
Surface finishing is a process that is used to improve the appearance and functionality of custom 2D metal parts. It is an important step in the manufacturing process, as it helps to improve the quality of the part and can help to improve the strength, wear resistance, and corrosion resistance of the part, as well as giving it a unique cosmetic appearance.
There are several ways to finish or coat cut sheet metal parts after fabrication:
1. Painting can be used to finish metal sheet parts.
2. Powder coating involves applying a dry powder paint to the parts, which is then baked onto the part. This method is often used for parts that need to be used in a harsh environment.
3. Anodizing creates a durable, corrosion-resistant finish on aluminum parts. This is a chemical and electrical process which causes a thin oxide layer to form on the surface of the parts.
4. Electroplating involves applying a thin layer of metal to the surface of the parts.
5. Passivation creates a corrosion-resistant finish on stainless steel parts.
6. Polishing uses abrasive materials to create a smooth, shiny surface finish on the parts.
The choice of finish or coating depends on the requirement of the part, the environment it will be used in, and the desired appearance.
Our Commitment to Custom Sheet Metal Quality
RCT MFG is ISO 9001 certified, demonstrating our commitment to maximizing customer satisfaction and continually reviewing our own processes to make improvements wherever possible. As part of our ongoing quality control program, we maintain documented procedures for effective application while ensuring we meet our customers’ manufacturing requirements. This helps us provide ideal solutions for both first-time and returning customers. While striving to have the best manufacturing processes, we also support our employees through education, training, and a safe work environment.
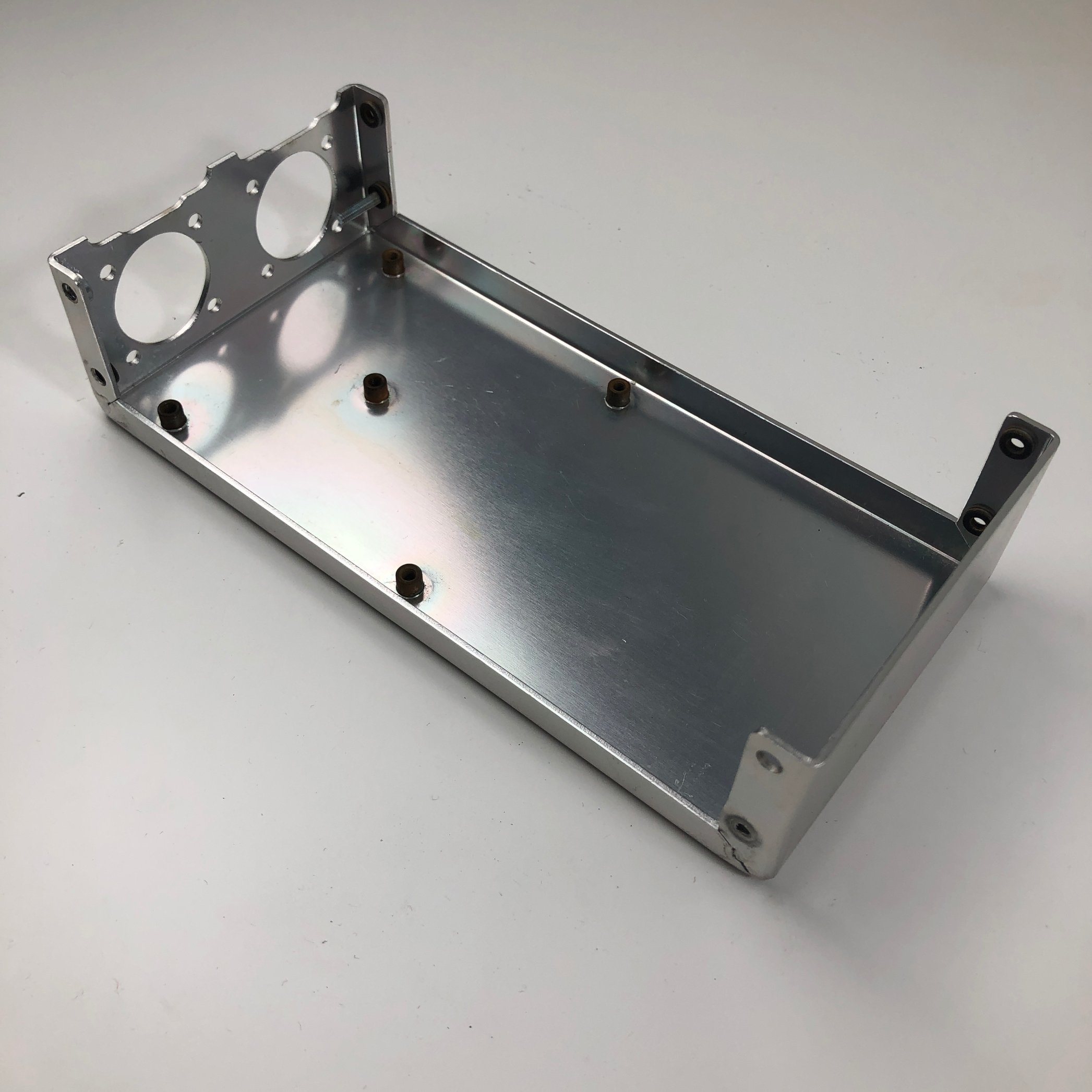
Have a project?
We specialize in tube, sheet, and plate fabrication. No matter the size of the job, we can handle it. Contact us today for a quote!